Preparación de pedidos
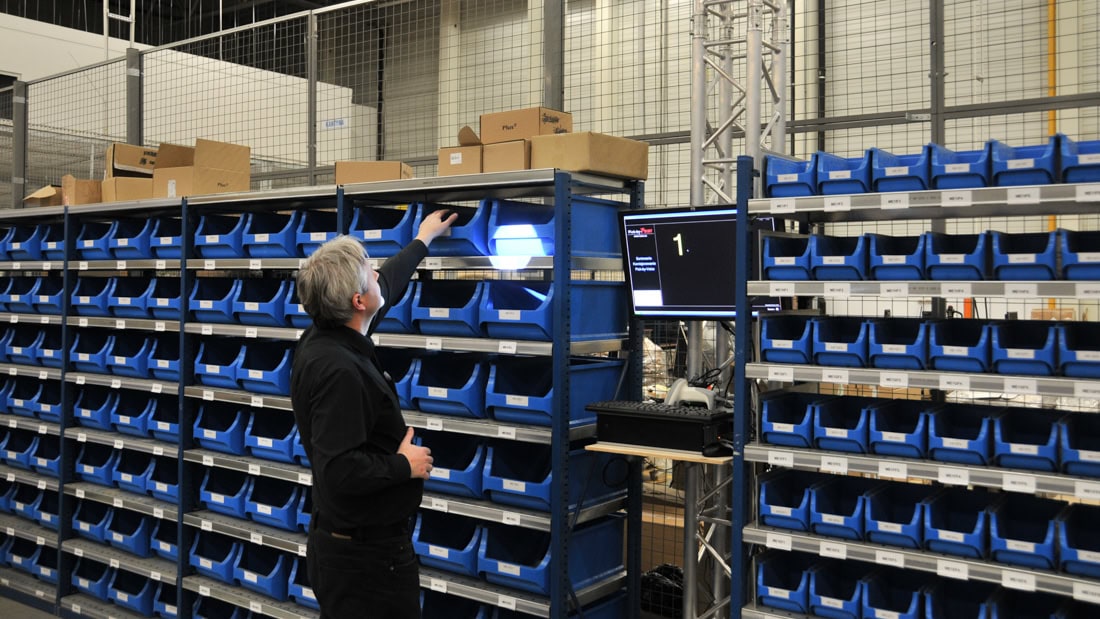
Las mercancías de un almacén de picking deben reunirse para su entrega en función de un pedido. Esta actividad se conoce como preparación de pedidos.
¿Qué es la preparación de pedidos?
El picking de mercancías es el proceso de combinar artículos de la cantidad total en un pedido. El sistema de gestión de almacenes controla las salidas de los compartimentos de almacenamiento utilizando varios métodos de picking.
En el artículo no sólo encontrará la definición o el significado de preparación de pedidos, sino también información importante sobre métodos y tiempos de preparación.
La selección de un vistazo
La agrupación de pedidos en un almacén o centro de producción la realizan manualmente los empleados (preparadores) o automáticamente los robots y máquinas de picking. La diferencia puede describirse básicamente del siguiente modo:
- Hombre a mercancía (manual)
- Mercancía a hombre (semiautomático)
- Preparación de pedidos totalmente automatizada
Preparación manual de pedidos
(hombre a mercancía)
En un proceso manual, las mercancías se reúnen con la ayuda de listas de selección o diversos sistemas de picking. El trabajo con papel se sustituye cada vez más por el picking sin papel. Los sistemas de apoyo guían al preparador de pedidos a los almacenes adecuados utilizando diversos métodos de picking. Le ayudan y supervisan la retirada de las mercancías.
El preparador de pedidos se desplaza por el almacén para recoger la mercancía de los palés, las estanterías dinámicas, las estanterías de baldas, etc. Por este motivo, el método se denomina hombre a mercancía. Por este motivo, el método se denomina " hombre a mercancía ".
Preparación de pedidos semiautomática
(mercancía a hombre)
El principio del método de picking semiautomático es inverso. La mercancía se transporta automáticamente en portacargas (contenedores o incluso estanterías enteras) desde el almacén hasta el puesto de picking y se pone a disposición del preparador de pedidos.
Por tanto, el preparador de pedidos permanece en su puesto de trabajo y tiene la tarea de retirar la mercancía de los portacargas en una cantidad adecuada y distribuirla entre los pedidos de los clientes. Por este motivo, el método semiautomático suele denominarse "mercancía a hombre".
Preparación de pedidos totalmente automatizada
En un proceso de picking totalmente automatizado, las máquinas y los robots de picking sustituyen por completo al empleado. Sin embargo, este método de picking solo es adecuado para determinados artículos, por lo que no solo la mercancía en sí, sino también la eficiencia económica desempeñan un papel decisivo en la selección del método de picking.
Los procesos totalmente automáticos suelen ser demasiado caros de adquirir y costosos de manejar y presentan una serie de desventajas.
En este artículo, le mostraremos qué métodos de picking manual (hombre a mercancía ) funcionan mejor. No nos limitaremos a darle consejos o definiciones, sino que le explicaremos exactamente por qué el picking sin papel tiene claras ventajas sobre la lista de picking convencional.
Los procesos de picking manual
Además de una lista de picking, hoy en día disponemos de muchos procesos de picking asistidos por sistemas. En función de las necesidades, pueden utilizarse distintos sistemas. Los mejores métodos de picking y los más utilizados son los siguientes
- Pick-by-Scan
- Pick-to-Light
- Voice Picking
- Pick-by-Point
- Pick-by-Frame
- Pick-by-Cart
- Pick-by-Watch
- Pick-by-Tablet
También existen algunas ampliaciones y soluciones especiales de LUCA Logistic Solutions:
- Pick-Radar
- Pick-by-Weight
- Pick-by-RFID
- Pick-by-ePaper
Puede encontrar todos los sistemas LUCA en el menú "Sistemas" o en la lista de la parte superior derecha. Todos estos sistemas están gestionados por un LUCA-Server central y también pueden utilizarse como combinaciones en la preparación de pedidos de una sola etapa. En este caso hablamos de soluciones híbridas. Con todos estos sistemas, las órdenes de picking pueden procesarse más rápidamente sin necesidad de familiarizarse por separado.
Horarios de recogida
Para que el picking manual sea eficaz y la entrega al cliente rápida, es necesario registrar y optimizar los siguientes tiempos en el proceso.
¿Qué es la hora de recogida?
El tiempo de recogida es la suma de los tiempos individuales necesarios para la recogida:
Tiempo de preparación de pedidos = tiempo base + tiempo de desplazamiento + tiempo de preparación de pedidos + tiempo auxiliar (tiempo muerto) + tiempo de distribución
Hora base
El tiempo base incluye las actividades organizativas previas y posteriores al proceso de picking:
- Impresión de las listas de picking desde el software de gestión del almacén (si no es en papel)
- Preparación de embalajes de cartón, contenedores, corlettes o palés
- Envío de los pedidos recogidos
Tiempo de viaje
El tiempo de desplazamiento define el tiempo que tarda el preparador de pedidos en desplazarse entre las distintas zonas de almacenamiento y compartimentos de almacenamiento. Este tiempo puede tener una gran influencia en el rendimiento global de la preparación de pedidos. Los factores más importantes son
- Tamaño de las zonas de picking y ruta hasta el siguiente punto de picking
- Orientación en el almacén para encontrar el compartimento de almacenamiento (pasillo, fila de estanterías, nivel de estanterías)
En este caso también debería investigarse siempre la posibilidad del método de Multi-Order-Picking .
Tiempo de agarre
Una vez que el preparador de pedidos ha llegado al compartimento de la estantería, se mide el tiempo necesario para acceder a la mercancía. El tiempo de preparación de pedidos también se conoce como tiempo de retirada o tiempo de picking. Incluye las siguientes actividades:
- Acceso a los artículos
- Contar las cantidades
- Almacenamiento del número de artículos en el contenedor de picking
La optimización del tiempo de preparación de pedidos y de la tasa de error suele estar vinculada a la ayuda del sistema para contar el número de artículos. De lo contrario, el tiempo de picking en sí no puede optimizarse en gran medida y también depende del tipo de almacenamiento de los productos (espacios para palés, estanterías dinámicas, estanterías de estantes, etc.).
Tiempo auxiliar (también conocido como tiempo muerto)
Antes de que el preparador de pedidos pueda acceder a la mercancía, se llevan a cabo otras actividades de procesamiento adicionales que también deben tenerse en cuenta. Por ejemplo
- Búsqueda de compartimentos
- Apertura y cierre de las cajas o contenedores del compartimento de almacenamiento
- Subirse a escaleras o utilizar medios auxiliares
- Registro de los números de serie, si es necesario
- Embalaje de seguridad de los artículos
- Acuse de recibo de la retirada
- Aplicación de etiquetas y rótulos
El tiempo no productivo (tiempo muerto) depende en gran medida de los pasos adicionales que requiera el proceso y también puede optimizarse. El tiempo de familiarización no se tiene en cuenta.
Tiempo de distribución
El tiempo de distribución incluye actividades no productivas que dependen en gran medida de la motivación de los empleados y de su actitud hacia el trabajo. Entre ellas se incluyen
- Pausas para necesidades personales (WC, fumar)
- Conversaciones innecesarias con compañeros de trabajo (a menudo sobre temas privados).
- Esperando las próximas instrucciones de los superiores
- Esperar las reacciones del sistema (por ejemplo, debido a controles lentos y procesos no optimizados).
Optimizar el tiempo de distribución está estrechamente relacionado con la organización, la motivación de los empleados y el ambiente de trabajo.
Métodos de selección
En la práctica, el objetivo es optimizar la distribución y la organización de los tiempos de procesamiento de los pedidos para recoger el pedido de un cliente de forma rápida y rentable. Por este motivo, los procesos de organización se diseñan a menudo de forma diferente para minimizar el esfuerzo. Los métodos básicos incluyen las siguientes variantes de métodos de picking:
Picking en serie orientado a pedidos
El pedido de un cliente es procesado uno tras otro en diferentes zonas de almacenamiento por uno o varios mozos de almacén. Este método de preparación de pedidos es sencillo y no requiere una organización compleja. La familiarización y la definición de responsabilidades de los preparadores de pedidos son sencillas. Las desventajas de este método son los largos tiempos de desplazamiento (largas rutas de picking) y la transferencia no regulada de los pedidos a la siguiente zona de picking. El tiempo total de preparación de pedidos no es óptimo.
Recogida paralela orientada a pedidos
Cada pedido se divide en varios pedidos parciales para que los artículos puedan fusionarse en paralelo. Los pedidos pueden dividirse en pedidos parciales según diversos criterios, por ejemplo, según las zonas de almacenamiento, el volumen de artículos para el transporte, los criterios de embalaje, etc. Tras el picking, los pedidos parciales se fusionan.
Los tiempos de preparación de pedidos son considerablemente más cortos en la preparación paralela orientada a pedidos que en la preparación en serie orientada a pedidos. Sin embargo, el flujo global de material, la organización de la fusión de pedidos parciales y la utilización desigual de las distintas zonas de almacenamiento son más problemáticos. Sin embargo, pueden controlarse bien con un sistema adecuado de control del flujo de materiales y tecnología de transporte automático.
Recogida en serie y en paralelo
Antes de empezar, los pedidos totales se resumen primero en serie y se distribuyen a las distintas zonas de almacenamiento en paralelo. Sin embargo, los pedidos no deben resumirse aleatoriamente, sino en serie, para que se realice un número máximo de recogidas por ubicación. Primero se recogen los artículos y después se distribuyen a los pedidos individuales.
La ventaja de este método de picking orientado a series es que sólo es necesario acceder a una ubicación una vez por serie y no por pedido individual.
Lea más detalles sobre los distintos métodos de pic king y descubra exactamente qué método de picking debe utilizarse en cada caso.
Esto ahorra distancias de desplazamiento y acorta el tiempo de procesamiento de los pedidos. Los artículos pueden distribuirse directamente durante la retirada con la ayuda de Pick-by-Cart o Pick-by-Frame®. La alternativa es la distribución posterior en puestos de trabajo especiales con Put-to-Point® o Put-to-Light. El método de picking orientado a series requiere un sofisticado soporte técnico.
Ejemplo de un proceso sencillo de preparación de pedidos
Los pedidos individuales se registran en un sistema de gestión de almacenes y los pedidos parciales se generan a partir de ellos. La recopilación (puesta a disposición o consolidación) de las mercancías para su embalaje o entrega para la producción se denomina entonces consolidación, que describiremos en detalle más adelante en otro artículo. En este caso, la organización del proceso puede ser muy diferente.
En los puntos siguientes, compararemos directamente un preparador de pedidos con una lista de picking en papel y un preparador de pedidos con picking sin papel y mostraremos las ventajas y desventajas en cada uno de los pasos. La familiarización es sencilla.
Inicio de los pedidos
En un proceso con lista de picking, el preparador toma la siguiente orden impresa y simplemente empieza a trabajar.
Las órdenes de picking sin papel se activan mediante distintos métodos, por ejemplo, utilizando lectores de códigos de barras (por ejemplo: albarán, unidad de recogida, contenedor o caja), RFID o activando las órdenes en un terminal MDE. La tecnología utilizada depende en gran medida del proceso deseado y del número de zonas de almacenamiento.
El inconveniente inicial de la preparación de pedidos en papel es que el albarán de picking puede perderse, lo que puede dar lugar a un error total en el procesamiento de los pedidos. Por este motivo, se instalan impresoras especiales para los albaranes de picking con el fin de evitar cualquier pérdida de órdenes de picking debida a la retirada involuntaria de los albaranes de picking, lo que ocurriría muy rápidamente con las impresoras de uso general.
La ventaja de la recogida sin papel es que la hora de inicio puede registrarse con precisión.
Visita guiada al almacén
Si el preparador tiene una lista de picking convencional en la mano, tiene que leer la designación del siguiente almacén, encontrar el almacén en la zona de almacenamiento y comprobarlo visualmente. Inconveniente: aquí suelen producirse errores tras muchas horas de trabajo, lo que conlleva graves pérdidas de calidad.
Con el picking sin papel, el empleado es guiado visual o acústicamente hasta su compartimento de picking. Para garantizar la calidad, el operario debe confirmar el lugar de almacenamiento leyendo el código de barras o por voz, según el método de picking. Los métodos de picking mejores, más rápidos y más seguros son los siguientes Pick-to-Light, Voice Picking, Pick-by-Frame, Pick-by-Point y Pick-by-Watch. Los peores procesos de picking en un almacén incluyen aplicaciones con gafas inteligentes: Pick-by-Vision.
La clara ventaja sobre la lista de papel es la confirmación del almacén y la reacción directa del sistema ante un error. El alto rendimiento de picking se caracteriza por el corto tiempo de recorrido (tiempo de búsqueda).
Retirada de mercancías
Si el empleado ya ha llegado al compartimento de almacenamiento correcto con la lista de picking, debe encontrar de nuevo la línea de texto correcta y leer correctamente el número de artículos. La lectura del número de artículos es una de las mayores fuentes de error en la preparación de pedidos en papel. Aquí es donde la capacidad de concentración del preparador de pedidos durante varias horas es muy necesaria.
Con el picking sin papel, el empleado ve la cantidad directamente en el almacén o en su dispositivo móvil. Con el sistema guiado por voz, la cantidad se muestra en los auriculares. La ventaja es que el empleado puede concentrarse mejor en su trabajo y el sistema le informa del siguiente paso en el momento adecuado.
En ambos casos, el empleado debe contar él mismo la cantidad correcta. Para grandes cantidades, recomendamos el uso de balanzas contadoras y un sistema de Pick-by-Weight por peso.
Confirmación de la cantidad
La cantidad retirada se "tacha" en una lista de picking con bolígrafo o se anota la cantidad que falta, que luego hay que rehacer manualmente en el procesamiento de pedidos.
La cantidad retirada se contabiliza automática e inmediatamente en un sistema sin papel, lo que supone una gran ventaja.
Conclusión
Una vez completados todos los artículos de un albarán de picking, el preparador puede abandonar la zona de almacenamiento, empaquetar él mismo su pedido o entregarlo para su posterior procesamiento.
Conclusión
La finalización del sistema se realiza de forma diferente. En función del proceso de picking utilizado, se informa al preparador y se le pide claramente que realice los siguientes pasos. Se registra la hora exacta.
La preparación de pedidos en el almacén es una de las actividades más importantes en una empresa de logística o producción. La calidad, la tasa de errores, el rendimiento del picking y la consolidación de cantidades parciales mejoran considerablemente con los sistemas de picking sin papel.
El sistema de gestión de almacenes puede realizar un seguimiento preciso de cada pedido del cliente en el proceso de picking. Existen varios dispositivos y sistemas de captura electrónica de datos. Hable con nosotros. Estaremos encantados de ayudarle a optimizar la preparación de pedidos.
¿Tiene más preguntas sobre la preparación de pedidos?
Hable directamente con nuestros expertos. Estaremos encantados de ayudarle.