Pick-by-Weight
A counting scale in conjunction with Pick-to-Light helps with the picking of large quantities, increases and ensures quality. The integration of different scales is easily possible in the LUCA-Server . A scale directly in the picking process ensures quality much better than a weight check of the entire consignment in the final inspection.
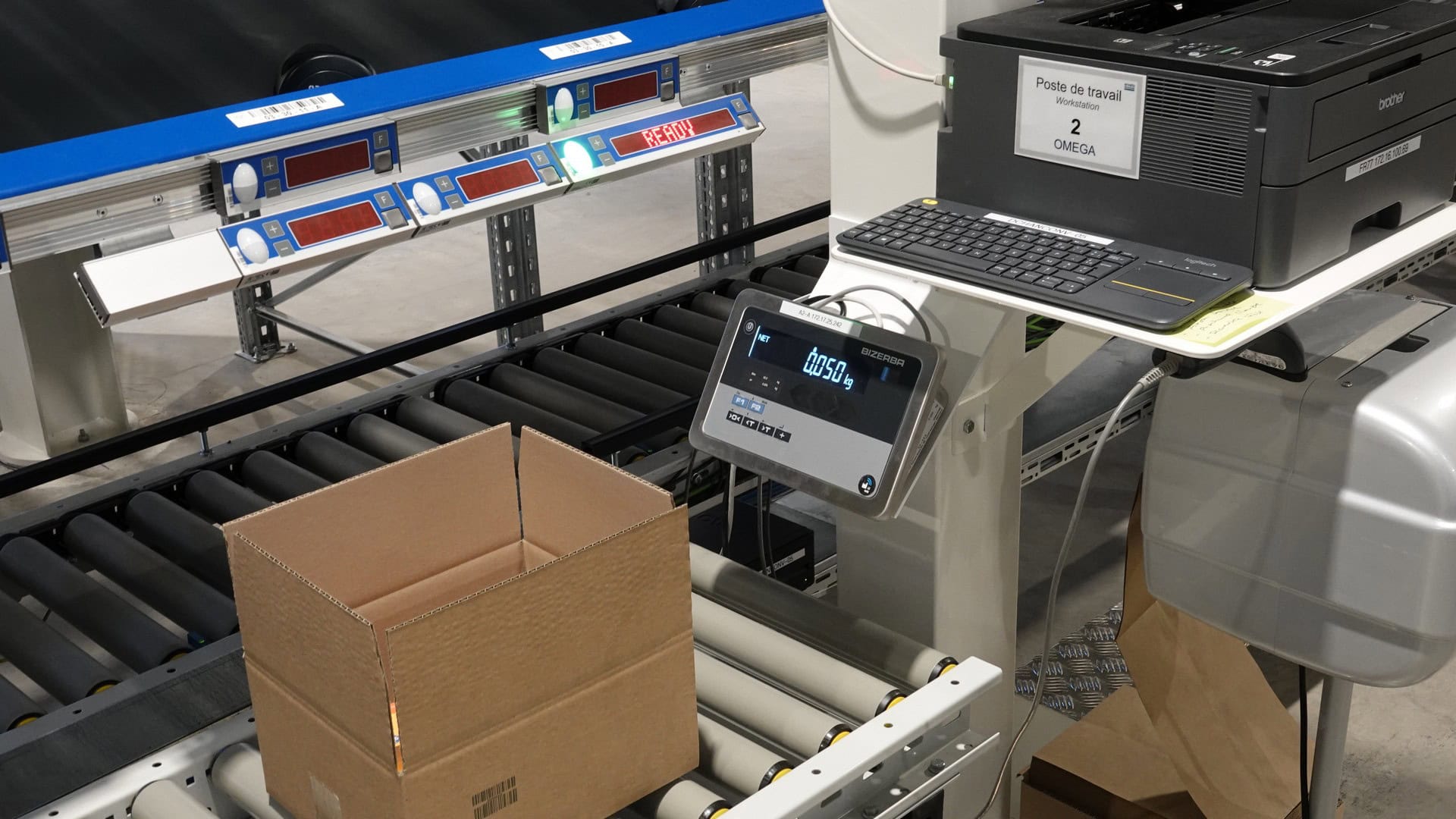
The weighing process and calibration are supported directly by the LUCA system
With the help of various picking systems, e.g. Pick-to-Light the removal compartment and the number of items are signaled. The removal is acknowledged on the display. The number of items in the picking compartment starts to flash and the tare of the scale is set to zero. The employee places the items on the scales. The "quantity remaining" is shown on the scale display. If the piece count is correct, the scale display shows "0" and the LED turns green. Any remaining quantity can be placed back in the flashing storage compartment and acknowledged. The process is not very fast, but guarantees very high quality. If required, a weight calibration of the items can be carried out at any time. We will be happy to provide you with the details in a personal consultation.
To count correctly with the scales, certain criteria must be met
The most important criterion for being able to use scales in the picking or shipping process at all is the stability of the weights for individual items. It is not possible to use a Pick-by-Weight for items where the weight cannot be determined precisely. If the items are stable in weight, the question then arises as to when it is best to weigh them. Unfortunately, there is no simple answer to this question. Many factors have to be taken into account.
List of questions for finding a solution:
- Are the weights of all items comparable or do they differ greatly?
- How large are the weight deviations in the tolerances of the individual articles?
- What quantities are picked?
- What performance must the process deliver?
- How can the workplaces be designed?
- Adaptation to any trolley possible
We can help you answer these and other questions in workshops.
Checking weights directly during order picking delivers the best results
It is often claimed that a checkweigher directly from the point of failure on the conveyor system is sufficient for the quality assurance of consignments. Unfortunately, this is rarely true. Without tare detection at the start of the conveyor line, correct net detection is hardly possible. In the case of cardboard boxes, even humidity plays a very important role. Sometimes the weight of the lightest item is within the weight tolerances of the heavier items, which makes correct weight verification impossible. For this reason, it is best to use the checkweigher directly during the picking process and not at the end. When calculating the total tolerance, at least half of the lightest item should always be taken into account. However, the result is not satisfactory because almost every consignment will then be incorrect