Pick to Light
We supply systems with
Pick to Light
for order picking, assembly and production.
The advantages of paperless picking are known to all professionals. Save time and money, increase quality and performance. No matter whether your company is small or large. In modern warehouse logistics, efficient order picking plays a decisive role in ensuring smooth processes. With advanced processes such as
Skarbecki
Reading time 15 minutes
What is Pick-to-Light?
Pick to Light refers to a process for order picking in warehouse logistics. For this, a Pick-to-Light with electronic compartment displays, which shows the picker the removal quantities directly at the storage compartment. The quick confirmation of picks with the acknowledgement button guarantees very high efficiency. The
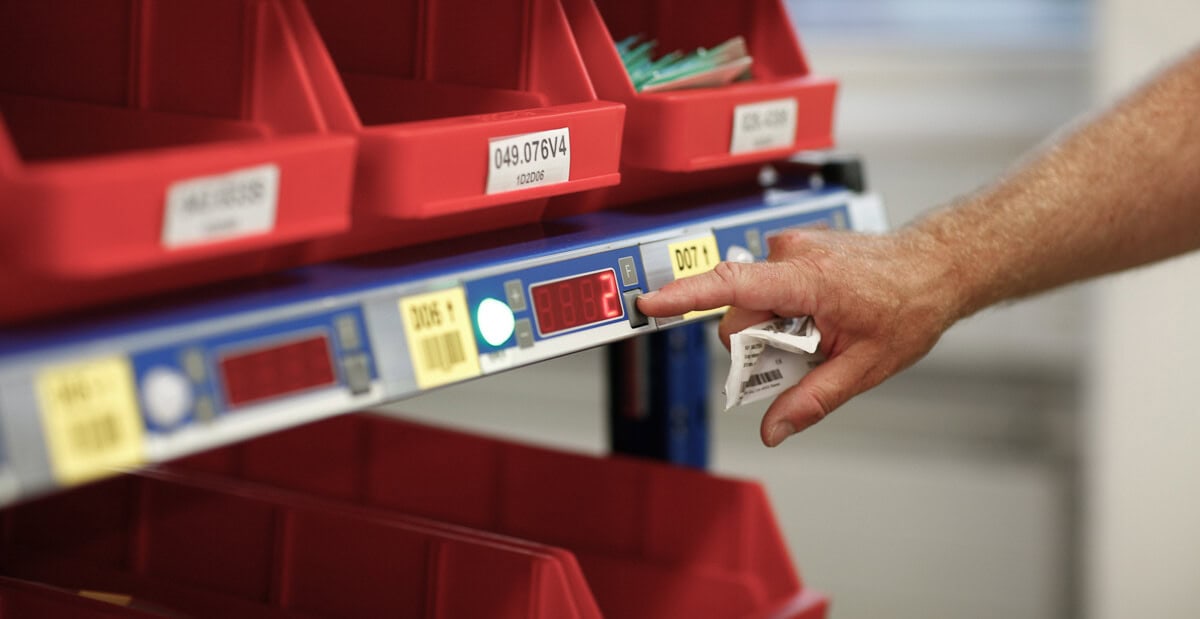

The mounting rails can be connected flexibly as a BUS or in a star configuration with the network-compatible controllers via
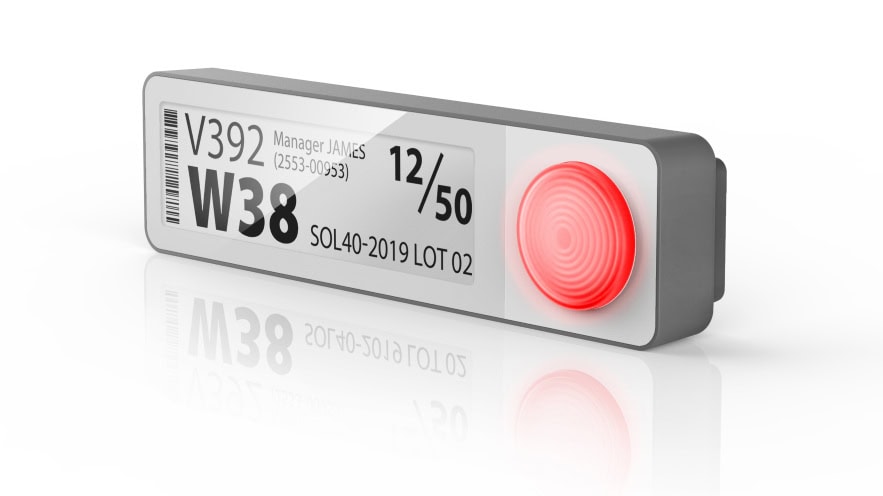
Modern wireless technology and ePaper completely replace cabling. The batteries power the compartment displays for several years. An excellent and very flexible solution for medium-sized systems.
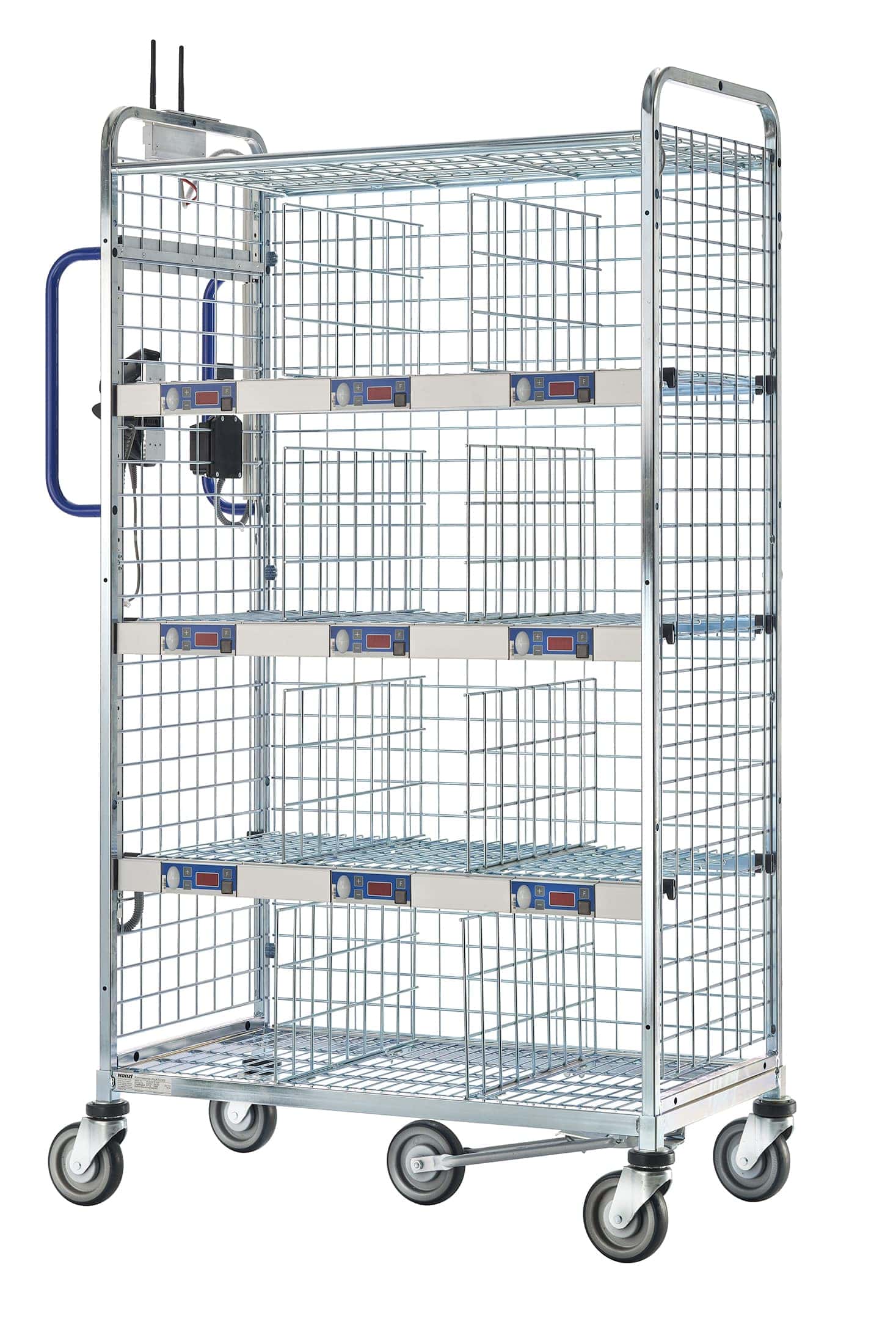
Each picking trolley can be equipped with Pick-to-Light for Multi-Order-Picking . The order picker is optimally guided through the warehouse and distributes the items to the target compartments quickly and reliably.
In this comprehensive guide, we help you to find the best solution for your modern and efficient picking process. Here we have compiled the most important types of Pick to Light, as well as the advantages and disadvantages of picking without a pick list. With this comprehensive information, we will help you make your purchase decision for
Procedure with step-by-step explanation
Thanks to Pick-to-Light , the picker does not need to waste time constantly looking at the picking list. The illuminated compartment displays show him the most important information directly at the storage compartment. A rough process can be summarized as follows:
- Picking, assembly or sorting is activated.
- The Pick-to-Light light up and show the removal quantities.
- The order picker carries out his activities and confirms them directly with the confirmation button on the storage compartment.
- Stock changes are posted immediately in warehouse management.
Wired
Pick-to-Light
We offer over 120 variants of high-quality, wired Pick-to-Light with various options. All shelf displays are always equipped with a double, 7-color LED. The selection of the right shelf displays and their features depends heavily on the requirements.
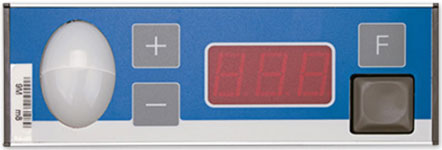
The classic in warehouse order picking in 2025.
The 3-digit quantity display shows removal quantities with a maximum of 999 pieces.
Type | PTF-3N-4 |
Height | 50 mm |
Width | 130 mm |
Depth | 25 mm |
Display | Red 3-digit, 7-segment display with high luminosity, dimmable |
LED | Two, horizontally divided, 7-color strong signal lights |
Keys | Robust acknowledgement button, plus, minus and F button |
Sensor | Optional: as automatic access recording. Find out more here: Pick-to-Light |
Areas of application | Storage compartment display for paperless picking, assembly stations, sorting, sequencing, set formation, shelves and pallets, Multi-Order-Picking |
Performance | Up to 350 picks per hour |
System | Suitable for order picking, assembly and production. Control via LUCA software. |
Costs | On request |
Hardware: Structure, installation, options
The Pick to Light hardware guides the order picker with light and consists of:
- Controller (communication and power supply)
- Mounting rails with integrated BUS (marked yellow in the graphic)
- Compartment displays with signal lamps (2 x 7 colors), quantity display and an acknowledgement button
- Cabling with 4-core cable between the mounting rails and controller
Installation, assembly and commissioning are very straightforward. The system is optimally prepared and suitably designed for this. Configuration is carried out directly on the displays. Conversions and extensions are child's play and can be carried out by trained personnel themselves.
The system is one of the best in order picking, is modular and very flexible. The installation and assembly of the displays at each picking location is simple and subsequent conversion options are uncomplicated. This is where KBS comes into play. Racks or mobile constructions are ideal for this. Regular maintenance is recommended and ensures the quality of order picking in the long term.
The functions are clearly structured and the light signals are unambiguous. The system supports various barcode scanners, RFID readers and scales.
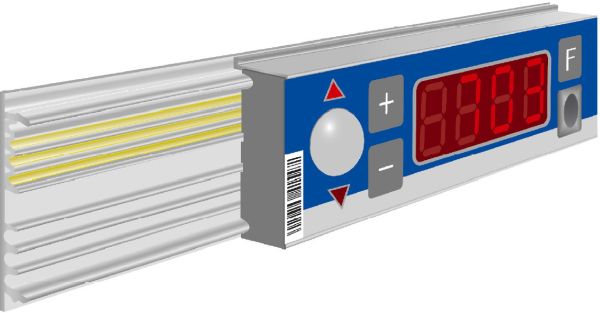
Further options:
- Sensor for automatic acknowledgement monitors access to the storage compartment (access monitoring).
- Digital I/O for receiving and transmitting external signals.
- Beep tone
The system is controlled by the LUCA software in real time. The connection to the higher-level system, material flow and conveyor technology is made via the LUCA-Server, which controls the entire process.
Error prevention with the innovative sensor directly on the Pick-to-Light compartment display
The pick-to-light sensor has an important new function for removal confirmation. It can be optionally installed above or below the display. The sensor monitors the accesses and also automatically confirms the activities. The installation of the sensors must be precisely coordinated. As a light sensor, it can measure 15-20 cm without a reflective mirror. With a reflective mirror, even 80-100 cm is possible.
Find out more about the Pick-to-Light.
Wireless Pick-to-Light
A wireless Pick-to-Light system is a solution where each Pick-to-Light is equipped with a battery, radio transmitter and radio receiver. In the area of use (e.g. a warehouse), additional bidirectional antennas are wired and installed for data communication with the wireless shelf displays.

This solution is very interesting for mobile installations where a lot of flexibility is required. Although the response times are much slower than with a classic Pick-to-Light, they are sufficient for some processes. The battery change justifies the simple solution.
Setting up the infrastructure with the permanently installed antennas is also manageable for small areas.
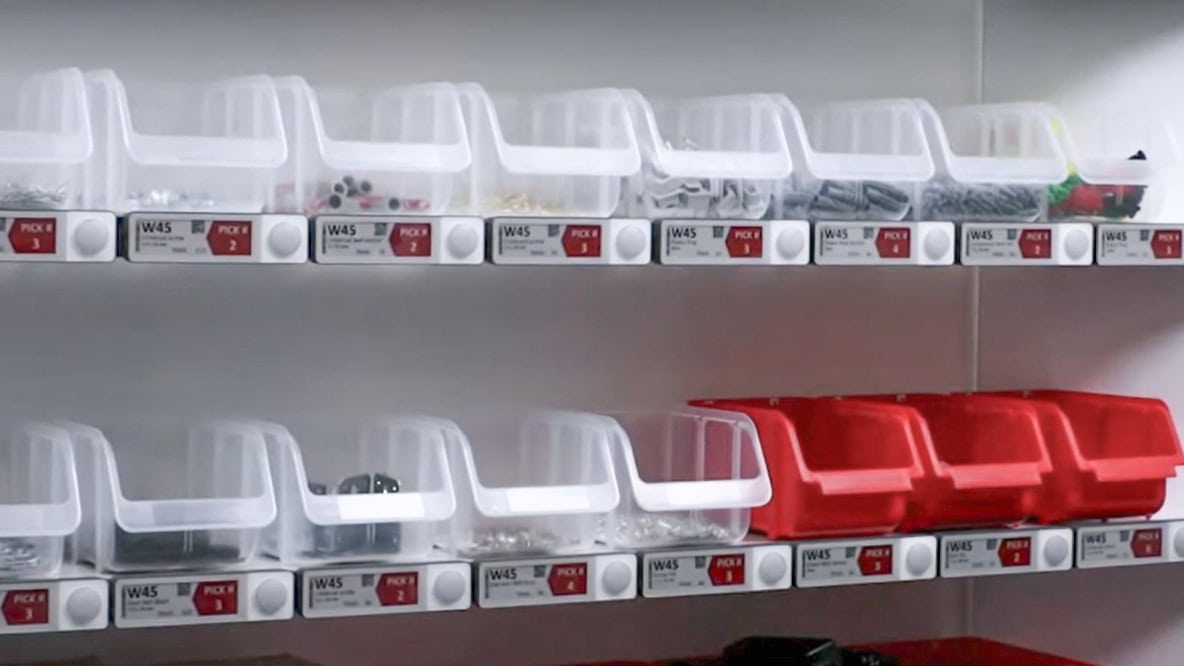
Our conclusion on the wireless Pick-to-Light
Das drahtlose Pick-by-Light System mit Vernetzungstechnologie ist für einfache, kleine (<100 Displays) und langsame Ablaufprozesse in der Kommissionierung von Sets und Montage sehr gut geeignet. Die Bauteile und Werkzeuge können damit schnell signalisiert werden.
Updating the content on the ePaper display takes approx. 20 seconds. The LED lights up within 2-3 seconds. For this reason, the use of wireless displays is very suitable for certain purposes (static display content), but does not replace the classic, wired Pick-to-Light.
For large installations (e.g. on shelves), classic, hard-wired solutions without radio are more suitable (see wired Pick-to-Light).
Mobiles Put-to-Light
Mobile use of the Pick-to-Light is of course possible on the picking trolley or on a mobile frame construction (frame). In this case, a replaceable, long-life lithium-ion battery powers the hardware components. The WiFi module provides the mobile data connection to the control system. Such solutions are known as Put to Light designated
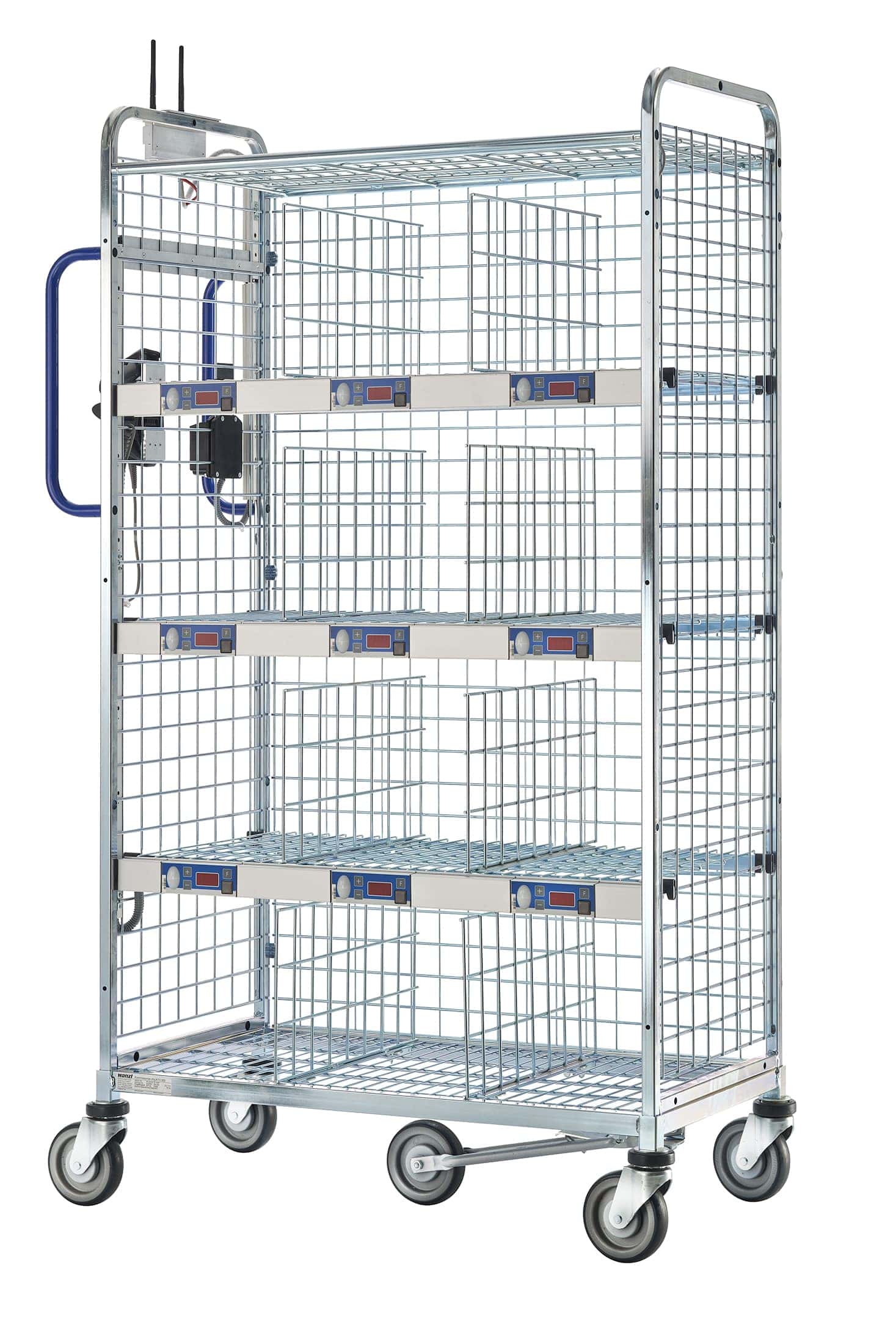

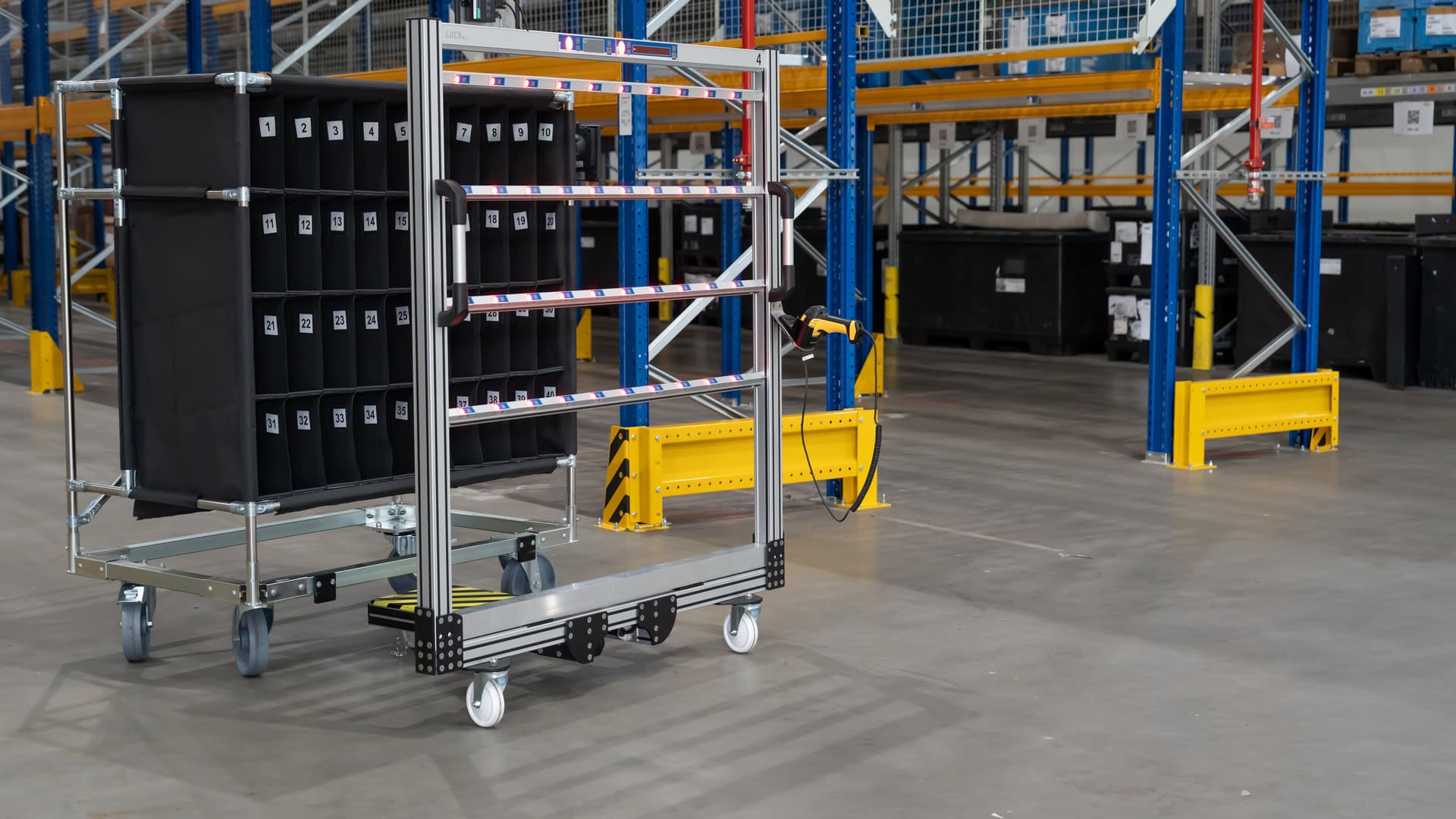
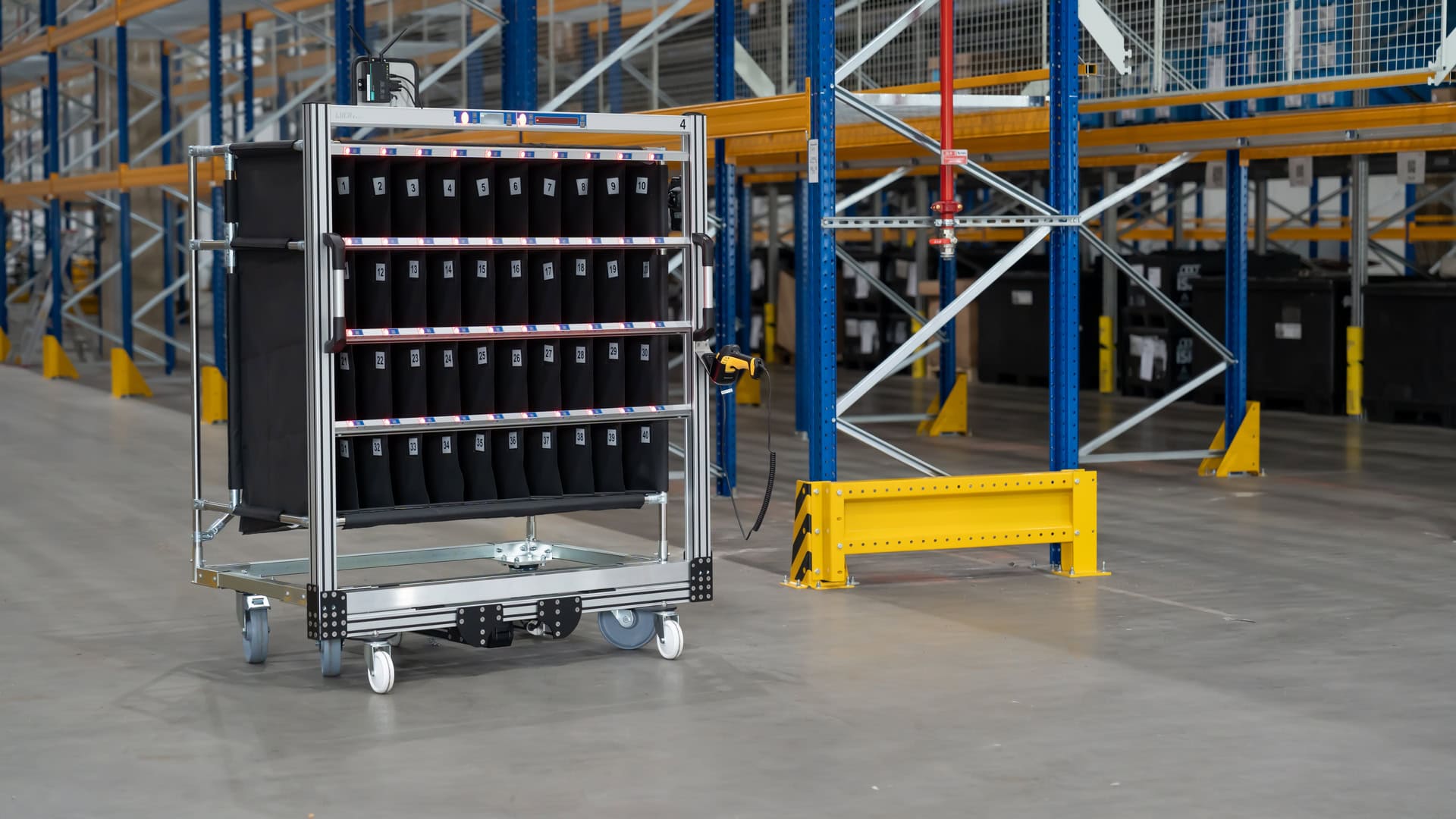
Connection of the Pick-to-Light
The flexible connection of the system to a higher-level system is crucial for an optimal process flow. This can be a warehouse management system, warehouse management system or ERP program. The advantages of a simple and fast interface are essential and have a major influence on many functions in the entire process.
Standard interface
The standard interface is realized via TCP/IP socket. Two asynchronous TCP/IP channels are set up for data transmission in both directions.
Communication channels for Pick to Light
The first channel (download) is used to activate and deactivate the displays. The telegrams contain many parameters. The second connection channel (upload) is responsible for the feedback of acknowledgements, corrections, special messages and error messages.
An acknowledgement of receipt is sent to each channel. This ensures that data is transmitted quickly and securely. You can find out more details in the article: Standard interface.
Customized connection
In some cases, the process and data supply must be optimized. We develop customer-specific connections for this purpose. Talk to us to find out more.
Software and commissioning
The Pick-to-Light forms a link between the hardware and the higher-level warehouse management system. It is installed on a Windows server provided by the customer and regularly checks the availability of the compartment displays. The entire picking process is also controlled in this software.
One of the most important aspects of good software is the response time and processing speed at the interfaces. The control system is based on the professional LUCA-Server which is very fast and supports different picking processes. The development is modular and very flexible. The process can be adapted very flexibly according to customer requirements
At the core of the software, only object-oriented ANSI C++ is used as the programming language. This guarantees high performance, stability and reliability.
The main functions of the software include
- Communication with the hardware and the warehouse management system
- Configuration of the system (e.g. assignment of compartment display designations in a warehouse layout)
- Monitoring and status messages in the event of faults
Operation is very intuitive and easy to understand. Thanks to the special configuration lists, even very large systems can be put into operation quickly.
On-site services
In order to integrate a Pick-to-Light smoothly, a number of prerequisites and on-site services must be fulfilled:
- Higher-level warehouse management system or production control system should be available (except stand-alone systems).
- Windows Server in the current version (e.g. as a virtual machine).
- database (Oracle, MS-SQL or Maria-DB) is only required for complex order management.
- Shelves with ergonomically prepared assembly surfaces.
- Ceiling suspensions if required (e.g. for free-standing pallet spaces without shelving).
- Cable trays with large shelf spacing.
- Power supply for the controllers 230V (16A) or battery chargers.
- LAN network or WiFi for mobile systems.
Areas of application and the most important differences
The following industries have been using our system for many years to support order picking tasks:
- eCommerce: picking warehouse, replenishment, sorting station in the dispatch warehouse
- Automotive: Batch processing and sequencing of shopping baskets and JIT racks for the assembly lines
- Production: assembly stations, set formation and machine loading
The pick-to-light system is a very versatile picking method that supports the picker and avoids picking errors. It has a wide range of applications. Further details can be found in the article: Where is Pick-to-Light used?
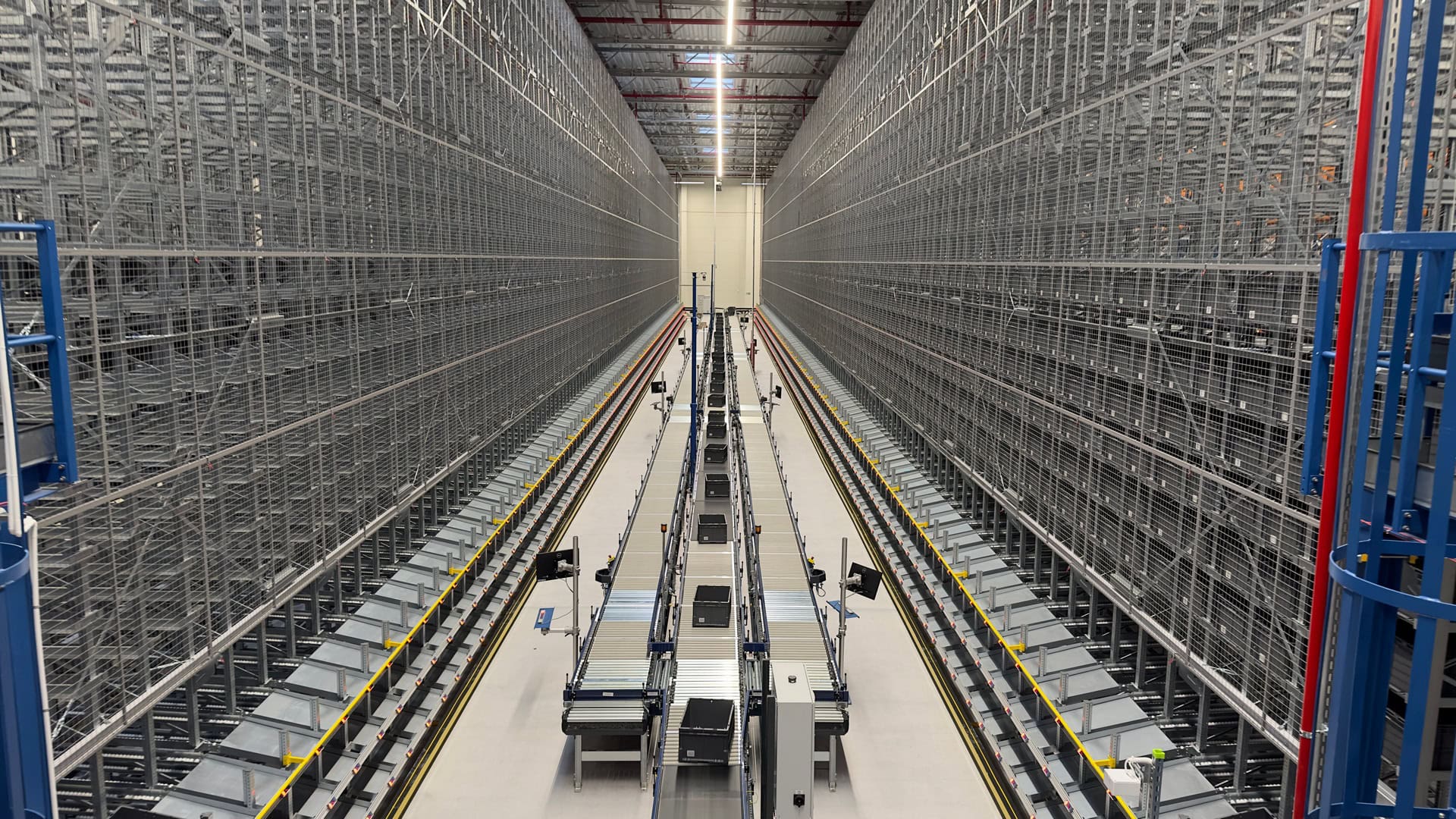
Differences between the individual types of compartment displays
The displays are equipped differently depending on the area of application. Each display is equipped with at least one LED signal light and one button. The other equipment features depend heavily on the different requirements.
In standard order picking in eCommerce, the display of the withdrawal quantity is mandatory. In a sequencing process in the automotive industry, the withdrawal quantity is constant (almost always equal to 1), so the quantity display can be omitted. On the other hand, additional information often needs to be displayed in production. Special display types are used for this purpose.
If you are not sure which display types are best for you, we will be happy to advise you.
The complete list of all display types can be found here: Pick-to-Light.
When does it really make sense to use a Pick-to-Light?
The system is not very cheap. For this reason, its use must be correctly planned and sensible. The system is best suited for:
- Fast order picking with high quality standards.
- Small and lightweight items that can be moved manually.
- Quickly changing articles (frequent stock transfers or new articles).
- Articles that are difficult to distinguish (e.g. during assembly and set formation).
- Changing personnel who need to be trained quickly.
We are happy to support you with your system planning. Please contact us.
Pick to Light in order picking
The paperless picking process is based on a pick list with picking orders. The warehouse management system transmits the data and distributes it to the appropriate picking areas of the picking system. There are many variants of how it works.
The standard process
LUCA has standard software in which the picking process from a storage bin already fulfills 80% of the pickers' requirements. The aim is to minimize the error rate and speed up the picking process. Very often, however, the requirements for the system are very specific.
Start of processing in Pick to Light
There are basically two different start methods here:
- Start via a document with barcode
- Start of paperless picking via FIFO or external triggers
If the delivery bills, boxes or containers are marked with a barcode, barcode scanners can be used directly. In this case, the displays can also be activated via the delivery bill or invoice. RFID technology is also supported.
Confirmation of removal at the acknowledgement button on the compartment display and end of order
Once all items have been picked from the storage bin, the picker confirms the removal directly at the compartment by pressing the confirmation button on the compartment display. This confirms the removal.
If the quantity is not correct, the correction buttons (+/-) can be used to correct the quantity. Confirmation of the removal triggers feedback to the higher-level warehouse management system (WMS).
Support in assembly and production
Assembly work often consists of many steps. The employee must correctly reach into many containers according to the assembly instructions. An assembly process with assembly instructions on a piece of paper is not ideal. The illuminated displays can significantly improve performance and quality.
You can find out more in the article: Pick-to-Light
Supplier and manufacturer
As a manufacturer, provider and expert in order picking solutions with Pick to Light , LUCA Logistic Solutions is very flexible thanks to the LUCA communication server software. We offer various technologies in order to achieve an optimal solution for the customer. We have been building our picking systems since 1998.
How good is Pick to Light and how much does the system cost at LUCA?
Performance and quality are opposing parameters. As a result, the more performance is expected, the less quality the picker can achieve and the error rates increase. Increasing performance and quality at the same time is not easy with any of the picking methods.
Faster and cheaper is the goal. The capabilities of the control software are crucial here. The simple conversion options are also important.
As a leading order picking process, Pick to Light provides us with an excellent example of how performance and quality can increase rapidly. Operator guidance is improved by the light signals.
The infrequent repairs or replacement of the specialist displays confirm the stability of the system. Any troubleshooting usually does not require the intervention of LUCA specialists.
Picking performance
Performance increases by up to 40%. The targeted support of access to the storage compartment also increases quality by more than 15%. This minimizes picking errors and teach-in time.
When using sensors, the quality increases by a further approx. 10%.
The ROI calculation and the costs
When planning the system, it is essential to consider cost-effectiveness and increased efficiency. Due to the low cost of the hardware, the procurement of the systems is relatively inexpensive. The costs for the projects are justified by the hardware costs. Expect a budget for the hardware of €60 to €100 per storage compartment (depending on the variant of hardware used).
An ROI calculation must show whether the investment is profitable for the company.
The big comparison between Pick to Light and Put to Light?
In this table, we have compiled the most important differences between the systems for you.
If you have never heard the term put-to-light before, read here first: What is Put-to-Light?
Properties | Pick to Light | Put to Light |
---|---|---|
Areas of application | Picking of individual orders, assembly and production | Replenishment, Multi-Order-Picking, distribution and sorting of goods, set formation |
Activation | Reading the order number (barcode, QR code or RFID) or automatically in conjunction with a conveyor system | Reading the article number in conjunction with a Multi-Order-Picking |
FIFO use | Yes, is possible | No |
Direction of activity | The items are removed from the storage compartments and placed in bins or boxes | The items are removed from containers or pallets and placed in the marked storage compartments |
Type of acknowledgement | Acknowledgement button or sensor | Acknowledgement button, sensor or mobile scanner |
Time of feedback | After the end of removal | Immediately after filing |
Special features of the structure | none | none |
Most suitable display types | PTF-3N-4, PTF-OL-1, PTF-S3N-3, | PTF-L-6, PTF-L-7, PTF-SL-3, |
Customized structure | Yes | Yes |
Pick to Light: advantages and disadvantages
We have compiled all the advantages and disadvantages of Pick to Light for you:
Advantages of Pick to Light: | Disadvantages of Pick to Light: |
---|---|
Short search time for articles | Relatively high acquisition costs (KBS) |
Hands free for order picking | Not suitable for free-standing pallets |
High freedom of movement and quality | Limited multi-user capability |
Language-independent | |
Increases efficiency and productivity | |
Reduces picking errors | |
High performance of the order picker and short throughput times | |
Fast quantity correction with direct feedback of stock changes to the warehouse management system |
Our conclusion
In logistics and production, the Pick to Light is one of the best and most widespread error-free picking systems. The picker intuitively follows the light signals and quantity displays at the picking location, thus minimizing his search time (operator guidance through the orders). Numerical and alphanumerical quantity displays show the number of items. The correction buttons help with stock errors.
The simple installation of KBS, robust acknowledgement buttons and flexible conversion options make the solution very attractive. Simple connection to any warehouse management system brings enormous benefits. The system can also provide excellent support for permanent stocktaking. Optimal operator guidance through customer orders is the goal.
In large warehouses with many storage compartments, however, the price of installing the displays is quite high.
Put-to-Light can also be used on the vehicle with WLAN to optimize picking times, travel times, etc. during order picking.
Find out more about Put-to-Light here: What is Put-to-Light?
The system is suitable for Industry 4.0 and is a leader in paperless picking.
You can find out more about the history in the article: "History and development".
The synonyms for Pick to Light are: Pick-to-Light, Picktolight, Pickbylight, Pick-2-Light, P2L
Further definition on Wikipedia.
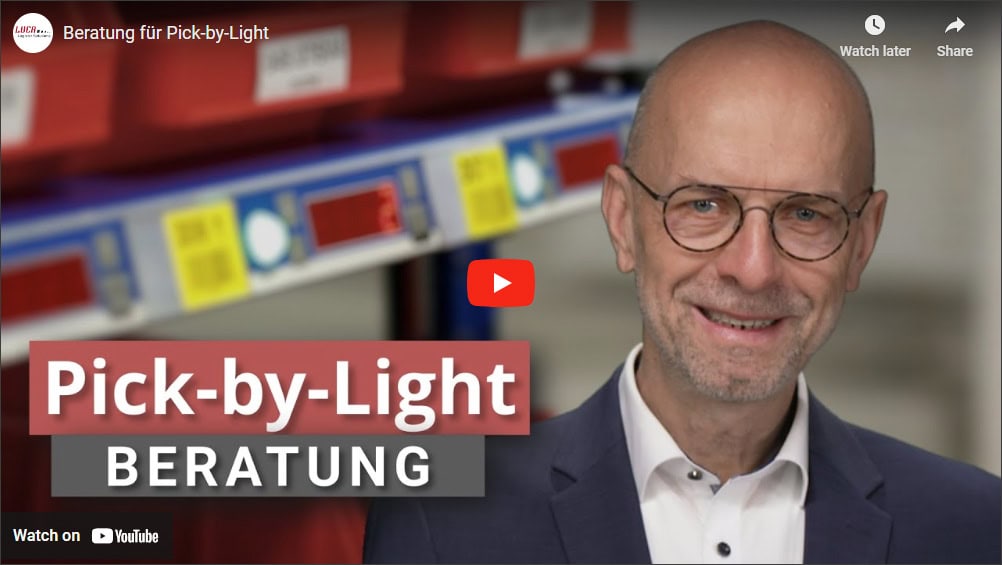
Top expert and consultant in the field of Pick-to-Light, order picking systems and classic material flow control systems. An innovative software developer and inventor of various systems.
Subscribe:
His motto: "The focus is always on a good idea and not just the technology."
FAQ
Pick to Light (or Pick to Light) is a warehouse logistics method for picking with the aid of light signals. The system with electronic compartment displays shows the picker the removal quantities directly at the storage compartment.
The costs depend on the number of shelf displays, the length of the shelves and the functions of the software. You should calculate a budget of €100 per shelf.
Further information on Pick-to-Light.
As soon as a picking order is activated, the compartment indicators light up and signal the removal compartment and the removal quantity from a great distance. The picker confirms the removal of goods (pick) at an acknowledgement button.
For a Pick to Light system, you first need the compartment displays, which are installed at each storage location. They contain LED lights, quantity displays and several buttons. Another system component you need is the controllers, which are used to supply the devices with power and data. Finally, there are the mounting rails, terminals and cables. The hardware from KBS offers the best flexibility. If you would like to find out more details, visit the page: Pick-to-Light in 2024 - LUCA Logistic Solutions.
The SAP interface is not implemented directly with the hardware, but via a server. The server communicates on the one hand with the compartment displays and on the other hand with the higher-level system, e.g. SAP or warehouse management.
The connection via a server can be flexibly configured with RFC, TCP/IP, databases, etc. Read more about this at: Pick to Light picking - LUCA Logistic Solutions
1. number and types of compartment displays (see: Pick to Light Hardware - LUCA Logistic Solutions)
2. number of mounting rails for attaching the modules
3. Total length of the mounting rails
4. Layout and functional description
5. Inputs to the host or warehouse management system