Assembly with Pick-to-Light
Pick-to-Light optimally supports assembly at an assembly table, minimizes errors and increases the quality and performance of employees. Freely configurable with many additional options. Connection to SAP or other systems possible.

Pick-to-Light
Assembly
How does Pick-to-Light support assembly?
- The assembly instructions are read in at a scanner.
- The Pick-to-Light light up for the first assembly step and show the quantities directly on the containers.
- The fitter removes the parts and confirms the installation on the push-button.
- Once all steps have been confirmed, the installation is complete.
Which Pick-to-Light displays are used for assembly?
Specialist displays
If the number of components in the assembly instructions always = 1, the display LED with push-button is used:
If several components have to be removed from a compartment in accordance with the installation instructions, the standard display with 3-digit numerical display is used:
The compartment displays are mounted directly above or below the bins. Removals from the individual compartments are acknowledged directly on the displays. Each installation step is acknowledged on a central button or the info display.
Info displays
Detailed information on the assembly process is shown to the employee on a central information display:
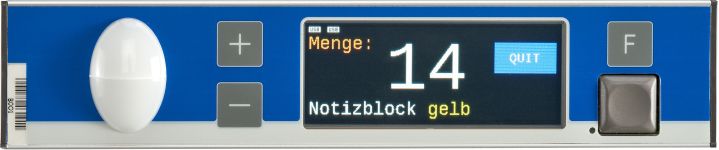
If screens are used at the table, the info display is not required.
You can find a complete list of possible displays in the article:
Option: Screens at the assembly station
If the assembly is very complex and the employee needs to see additional assembly instructions, assembly instructions, CAD drawings or images, screens are installed at their assembly station.
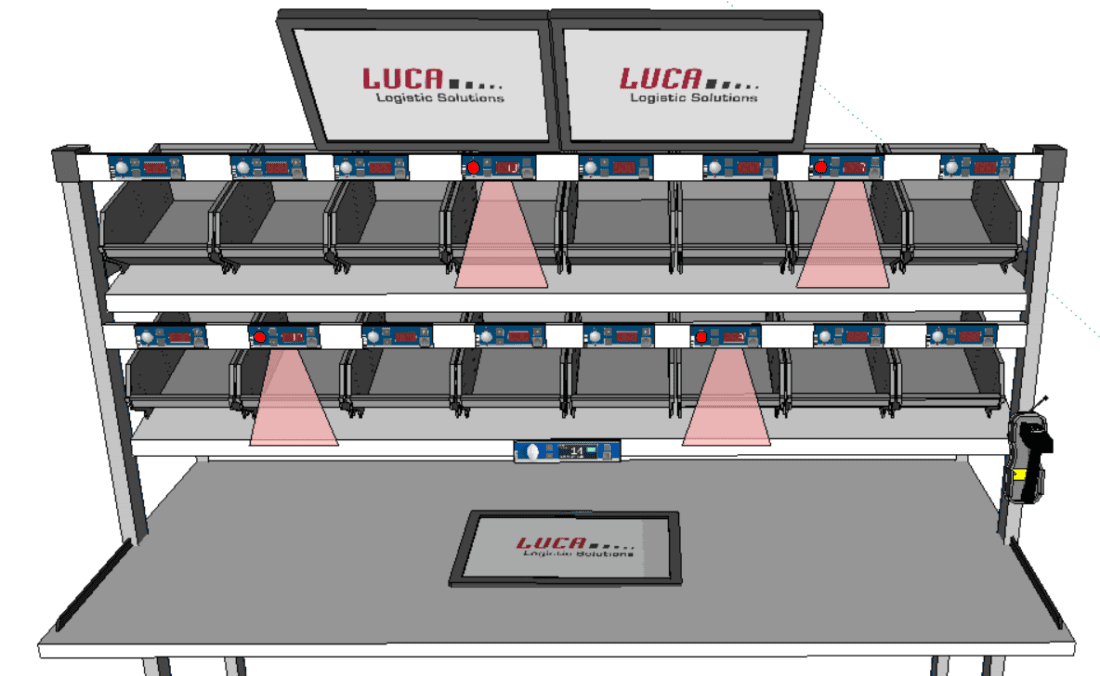
The position of the screens is always very individual and depends on the ergonomics of the assembly workstation. Various tools, test equipment and measuring devices can also be positioned on the table. The assembly table can be used as a test bench or test station.
Option: Sensors monitor the assembly
Optionally, each display can be equipped with a sensor for automatic access monitoring.
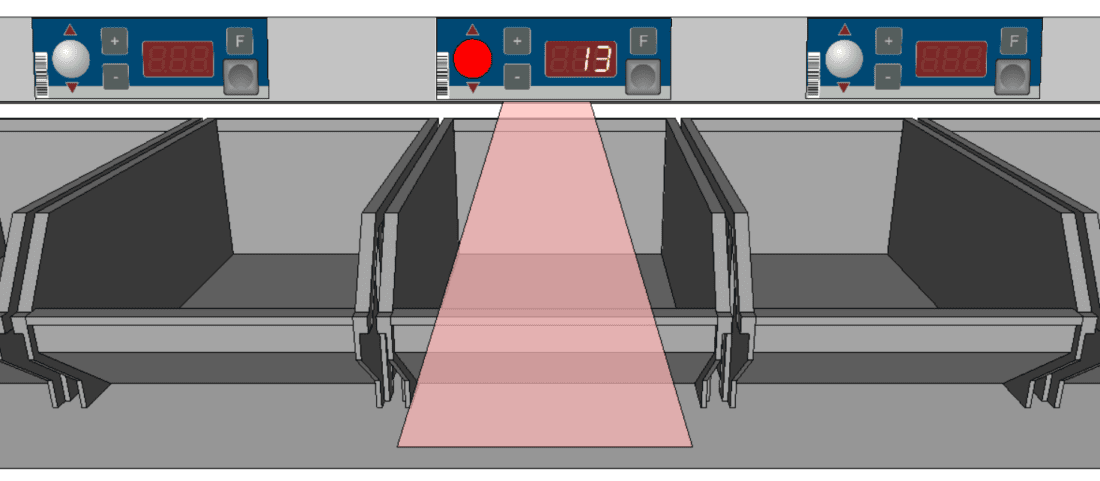
Acknowledgement with the button is only possible once the employee has reached into the compartment.
The sensor increases the quality of the removal.
If the number of items = 1, acknowledgement is automatic. For other quantities, the removal is acknowledged individually or centrally, but only if the active sensors have registered the accesses correctly.
If the employee reaches into the wrong compartment, an error message and signal tone are emitted.
Configuration of the assembly stations
If the connection to a production system is not available, the individual assembly steps must be configured manually.
- A special "Setup" barcode is read in to start the configuration.
- The unique barcode is then scanned to identify the assembly list.
- The info display shows the text "Step 1". The +/- buttons help you to select the steps. The configured Pick-to-Light on the compartments light up for each step.
- The compartment display acknowledgement button switches the individual displays on and off.
- The number of pieces can be set directly on the compartment using the +/- buttons.
- Once everything has been configured, the "Save" barcode is read in and the configuration is saved.
Configuration is very simple and requires no IT knowledge. The two special barcodes ("Setup" and "Save") are available to the installation manager.
Connection to a production system
A system-side connection to SAP or another production system is possible without any problems, but requires some coordination and possible customer-specific software adaptations.
Flexibility through dynamic containers
In some situations, a large number of different parts have to be provided on the table, depending on the assembly requirements and assembly step. However, space on an assembly table is very limited. The innovative Pick-by-Frame can be used as a solution.
First, the required containers are picked on a picking trolley in a picking warehouse.

A moving construction (Pick-by-Frame®) with mobile Pick-to-Light is docked onto the trolley for this purpose. The system guides the picker to the storage locations in the warehouse and supports him in distributing the components into the containers. The trolley is clearly labeled and managed by the production system.
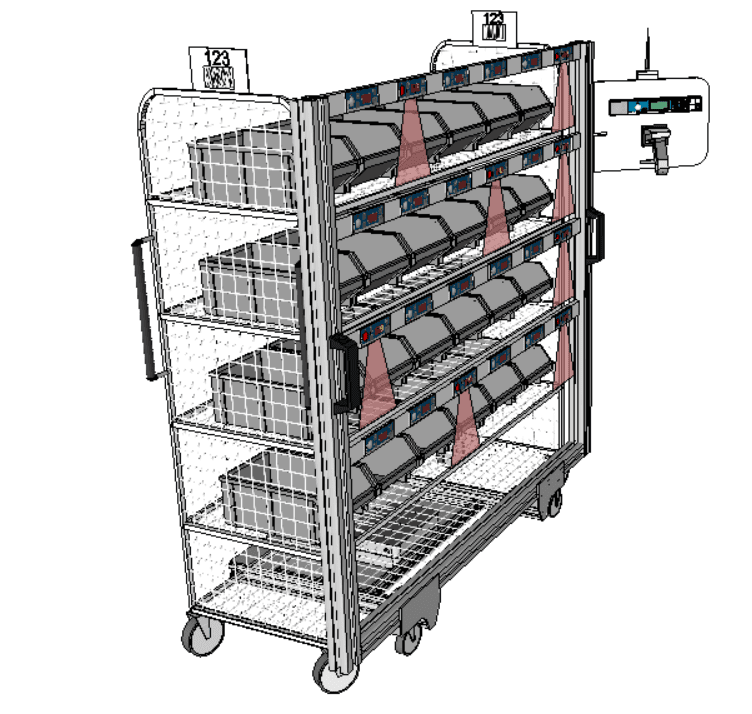
Once the picking trolley is ready, it is placed on a frame at the assembly station in accordance with the assembly list. The trolley is registered at the table using its barcode or RFID. Assembly only starts when the dynamic containers are correctly positioned.
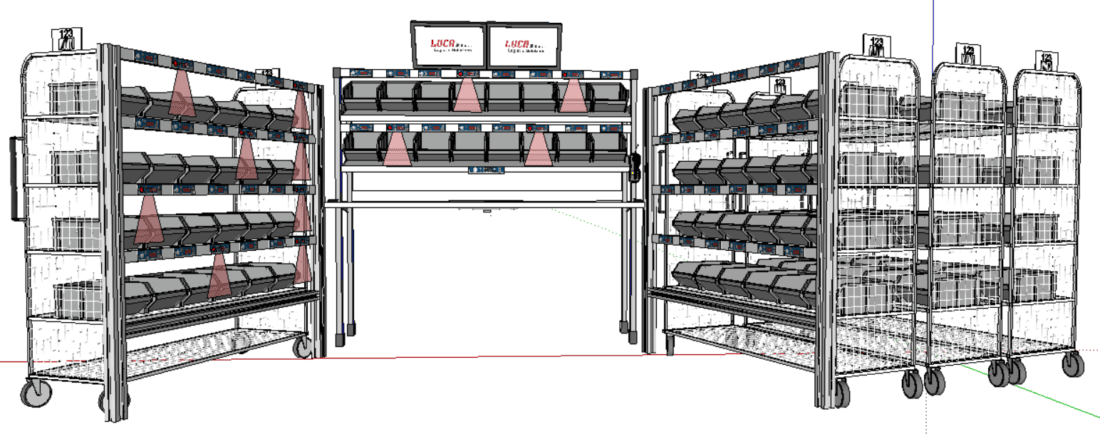
FAQ
Which assembly tables can be equipped with Pick-to-Light ?
Any assembly with containers or boxes can be retrofitted. The displays can be attached to any mounting location. If the compartments are very small, the small displays from the PTF-S series can be used.
How many Pick-to-Light can be operated on one assembly table?
The maximum number is not defined. A standard controller controls up to 150 displays. Several controllers can also be used at one assembly station. However, the workstation should be set up clearly and ergonomically. Therefore, there should not be too many displays.
Does the assembly table need to be connected to SAP or other systems?
No. The assembly table can also work without any connection to a higher-level system. The configuration of the assembly steps is then carried out manually and does not require any special IT knowledge.