Put to Light: distributing and sorting goods in 2023

In this comprehensive guide to Put to Light, we help you to find the best solution for modern, paperless sorting and goods distribution. Here we have compiled the most important features of two-stage picking with put-to-light, as well as the advantages and disadvantages of the process. With this comprehensive information, we help to make your decision to buy Put-to-Light as easy as possible. Enjoy reading!
What is Put to Light?
Put to Light with compartment displays is a very modern, light-controlled, paperless method for sorting, distributing and picking goods. The storage position of the stored goods is shown to the picker directly via a compartment display on the target compartment and confirmed with the acknowledgement button or sensor.
We supply state-of-the-art systems for
Put to Light
and help you immediately with a personal
online consultation.
Put to Light System: the most important facts in brief
- Put to Light is a reverse procedure to a Pick-to-Light.
- In a sorting process, the signal light shows the picker the exact storage position of the item.
- The sorting process is greatly accelerated by the light signals.
We'll find a solution together.
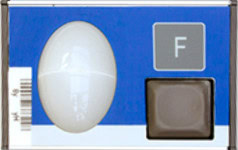
Type | PTF-L-6 |
Height | 50 mm |
Width | 70 mm |
Depth | 25 mm |
System | Very suitable for sorting and goods distribution. Control via Windows server with LUCA software. Linux on request |
Display | none |
LED | Two, horizontally divided, 7-color strong signal lights |
Keys | Robust acknowledgement button, function button |
Sensor | Optional: as automatic access recording. Find out more here: Pick-to-Light |
Areas of application | Storage compartment display for paperless sorting, goods distribution sequencing, two-stage picking |
Performance | up to 400 articles per hour |
Quality | 100% sorting with inserted sensor |
Costs | 90,- € as budget for the hardware per storage compartment incl. accessories |
learn more about PTF-L-6 |
How does put-to-light work in two-stage picking?
Before the start, a batch of orders is compiled in the warehouse management systemMulti-Order-Picking). In a two-stage picking process, the goods are first picked from the warehouse in several containers. The bins are then taken to the sorting station and distributed to several orders using the put-to-light system. Depending on the solution, there are two different sorting processes:
1. sorting with identical articles
If the picking system picks into the bins by type, then the same items are always in a bin. To distribute the goods, it is sufficient to read the bin barcode. The system then switches on all compartment displays on the sorting rack with the corresponding quantities.
The picker confirms that the items have been deposited by pressing the acknowledgement button. This method is only used for a small number of products.
2. collection boxes
In the first stage of picking, different items are first picked into the collection box. When the goods are distributed, the employee must read each item again and sort it separately. Acknowledgement at the acknowledgement button is identical. This process is slower than the first, but gives more flexibility with a large range of articles.
Entering the quantity in the put-to-light process
With some solutions, the items in the box can be grouped very easily (e.g. CD, DVD, etc.), which means that they have to be removed in groups and not individually.
In this case, the number of items can be entered on a screen at the sorting station. The barcode then only has to be read once during sorting. This saves a lot of time and money during sorting.
Sensors during acknowledgement
To improve the performance and quality of sorting, sensors can also be used on the compartment displays as an option. They automatically acknowledge the placement of items in the sorting compartments, providing feedback to the position management system without the need to press the acknowledge button. The increase in performance when using sensors is approx. +15%.
What is important with a put-to-light system?
The most important aspect of a Put to Light system is the reaction time after the barcode has been read. The order picker must not wait for the compartment display light. In our experience, the response time of the system must not exceed 250ms. Our communication serverLUCA-Server) guarantees the corresponding response times without any problems.
Advantages
The biggest advantages of put-to-light picking include
- Quick orientation of the employee thanks to the illuminated compartment displays (short search time)
- Direct display of the number of items in the storage compartment (target compartment)
- Direct acknowledgement of the deposit at the acknowledgement button or sensor and direct response to the warehouse management system
- Fewer errors, more performance
Disadvantages
However, the process also has some disadvantages:
- Low flexibility due to the fixed batch size (number of storage locations)
- Relatively high investment costs (as with Pick to Light)
Conclusion
Put-to-light solutions are processes in two-stage paperless picking, in which sorting takes place in the second stage with illuminated compartment displays. Seen in this way, it is a reverse Pick-to-Light in which the articles are not picked, but put according to the light signals. Read more about put-to-light on Wikipedia or contact us to find out more. We will be happy to advise you.